HIGHLIGHTS
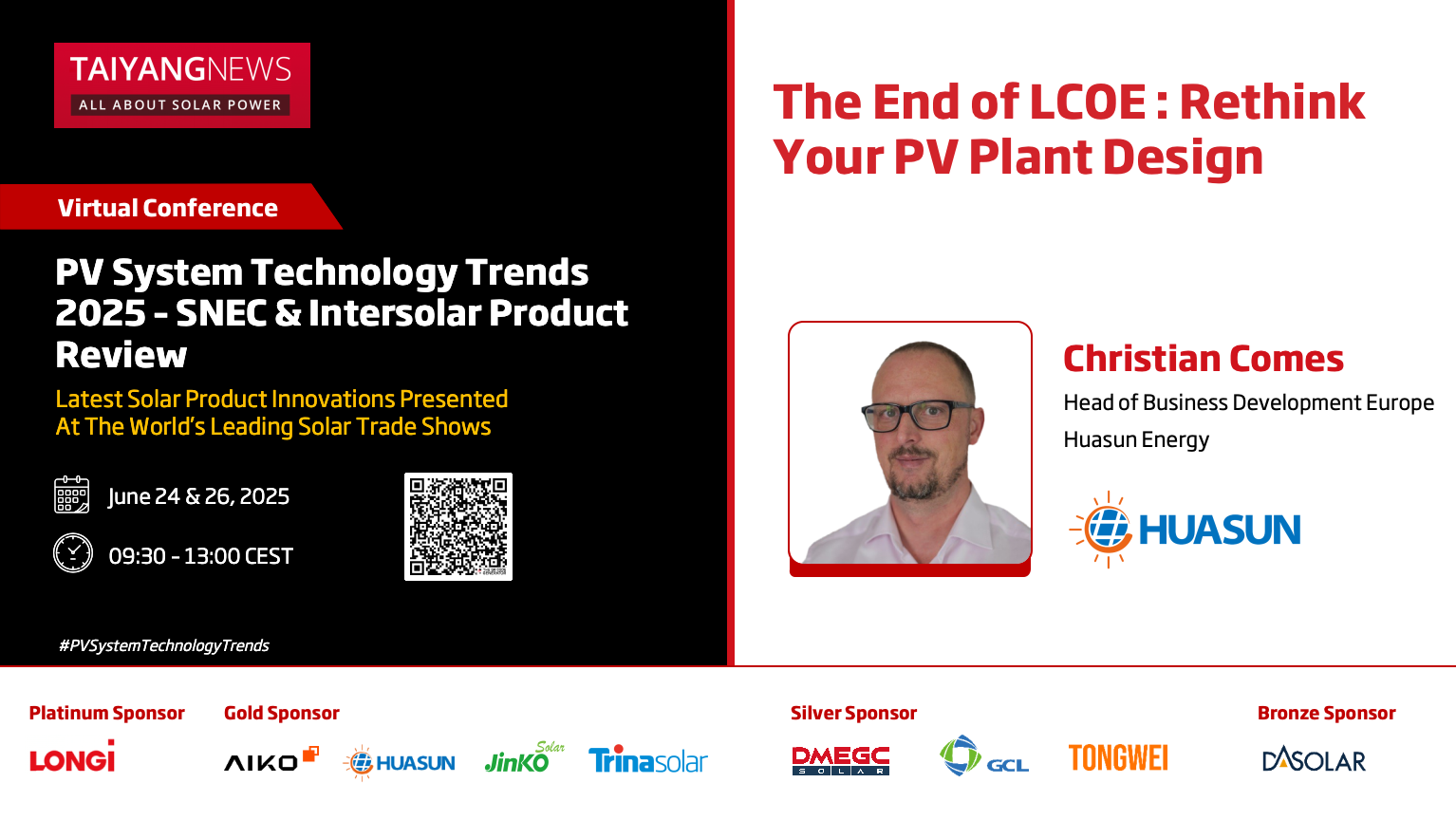
The End of LCOE: Rethink Your PV Plant Design with Huasun HJT Vertical Modules
2025-07-10
On June 26, the “Global PV System Technology Trends 2025” conference, hosted by TaiyangNews, concluded with insightful discussions on the future of solar energy. Christian Comes, Head of Business Development Europe at Huasun Energy, was invited to deliver a keynote titled “The End of LCOE: Rethink Your PV Plant Design.” Comes systematically addressed the potential limitations of profit models based solely on Levelized Cost of Energy (LCOE) for solar plants
Learn more
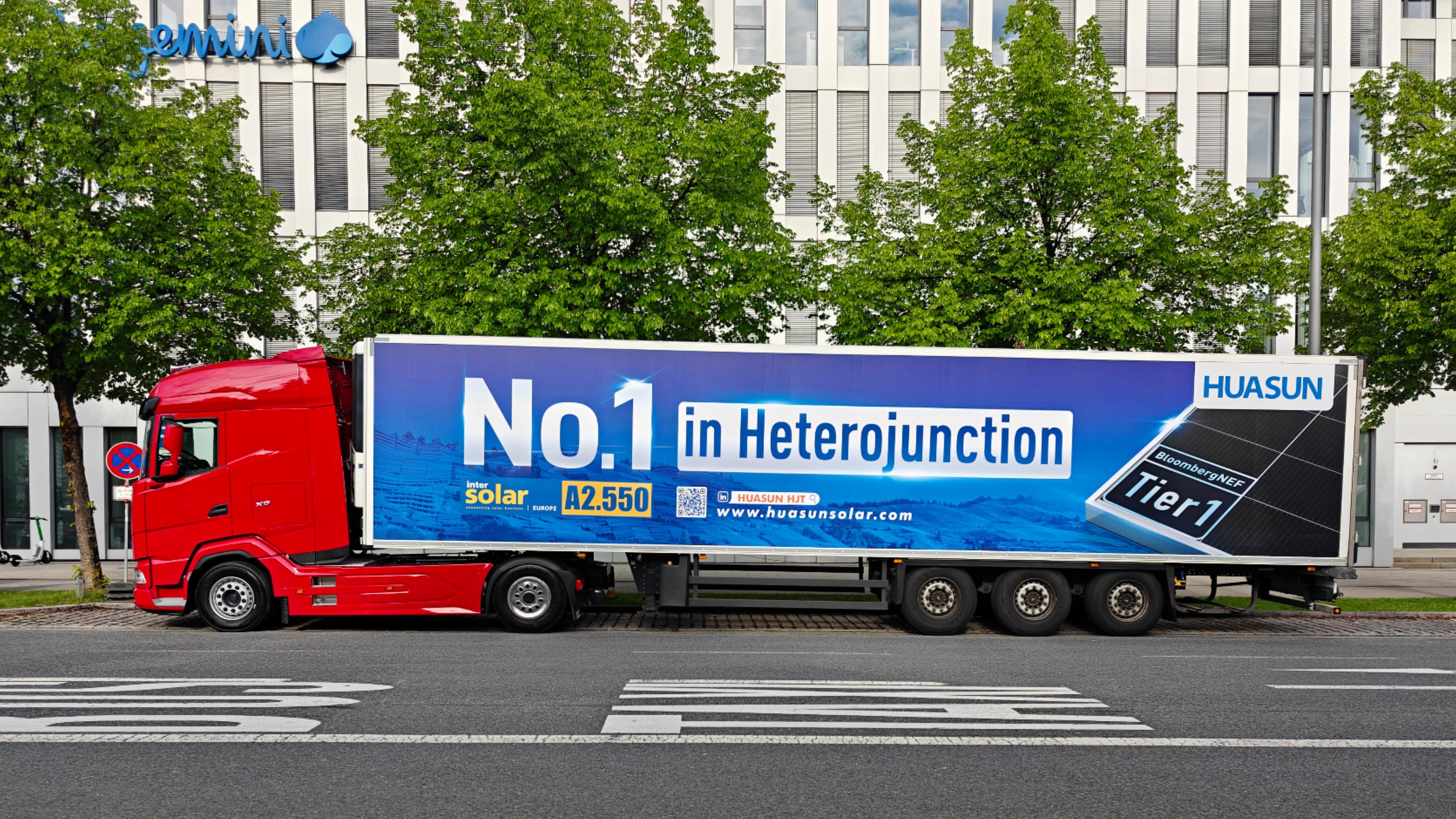
Huasun Wraps Up European Roadshow, Showcasing HJT Leadership and Vertical PV Innovation
2025-07-09
From April to June, Huasun brought its cutting-edge photovoltaic (PV) technology directly to the European market with a branded truck tour across Munich, Germany — spotlighting the company’s leadership in heterojunction (HJT) solar innovation. As a global leader in HJT technology, Huasun used the tour to spotlight its performance edge. One side of the truck carried a bold statement—“No.1 in Heterojunction”—supported by solid data: mass production of 730 W
Learn more
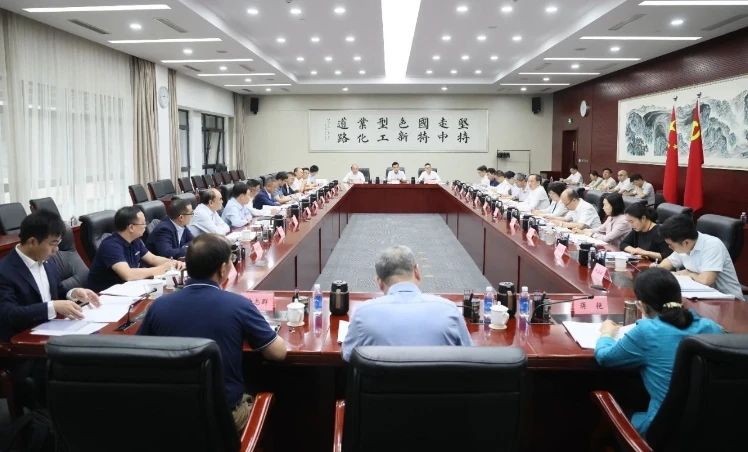
Huasun Energy Attends China’s Ministry-Led Talks to Boost High-quality Solar Growth
2025-07-08
On July 3, China’s Ministry of Industry and Information Technology (MIIT) held the 15th Symposium for Manufacturing Enterprises in Beijing, focusing on advancing high-quality development in the photovoltaic (PV) industry. The symposium brought together 14 leading PV companies, including Huasun Energy, and industry associations to discuss growth strategies. MIIT Minister Li Lecheng called for ending price wars, phasing out outdated capacity, and shifting to
Learn more
ALL
Select the year
ALL
2025
2024
2023
2022


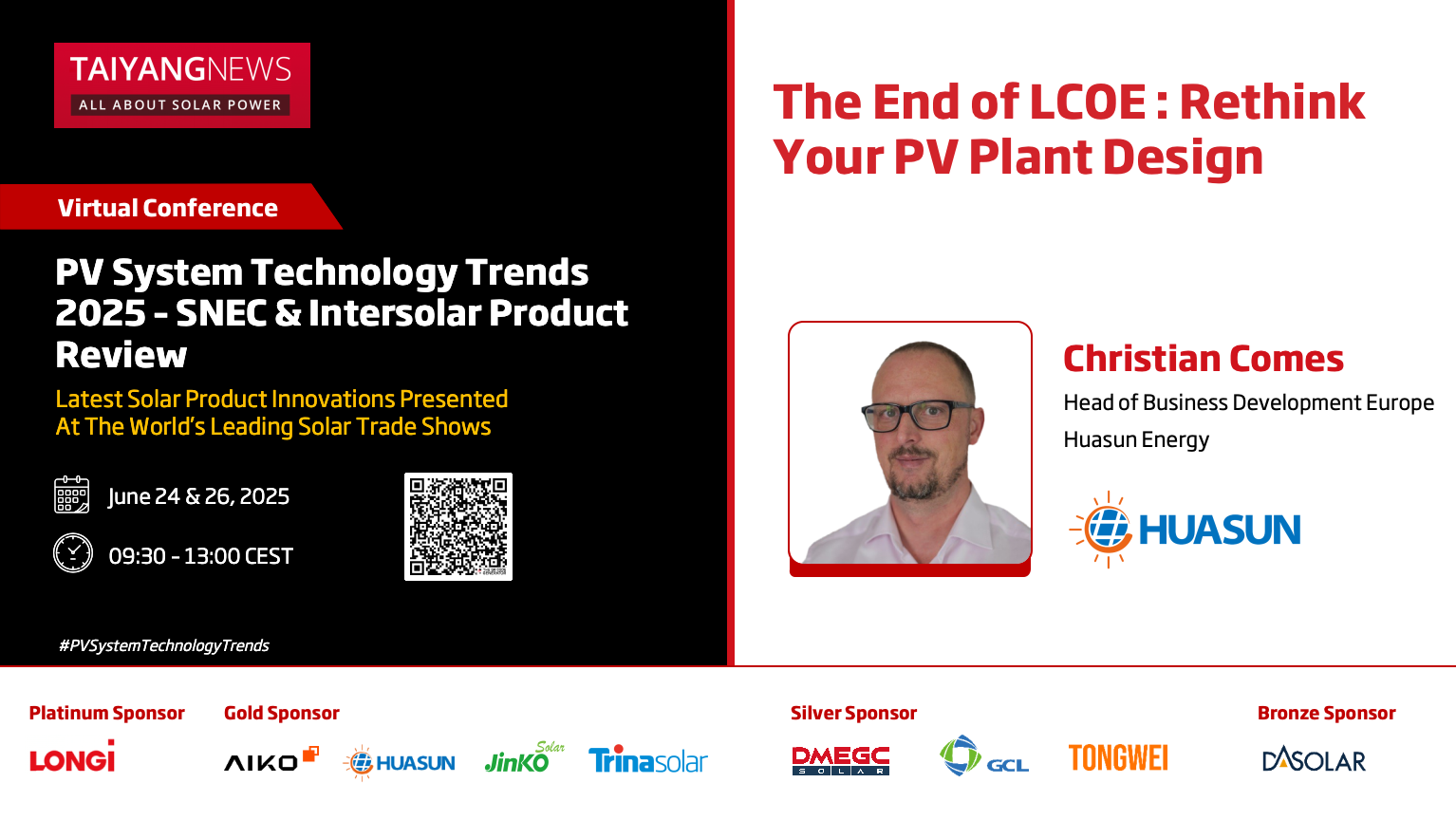
The End of LCOE: Rethink Your PV Plant Design with Huasun HJT Vertical Modules
2025/07/10
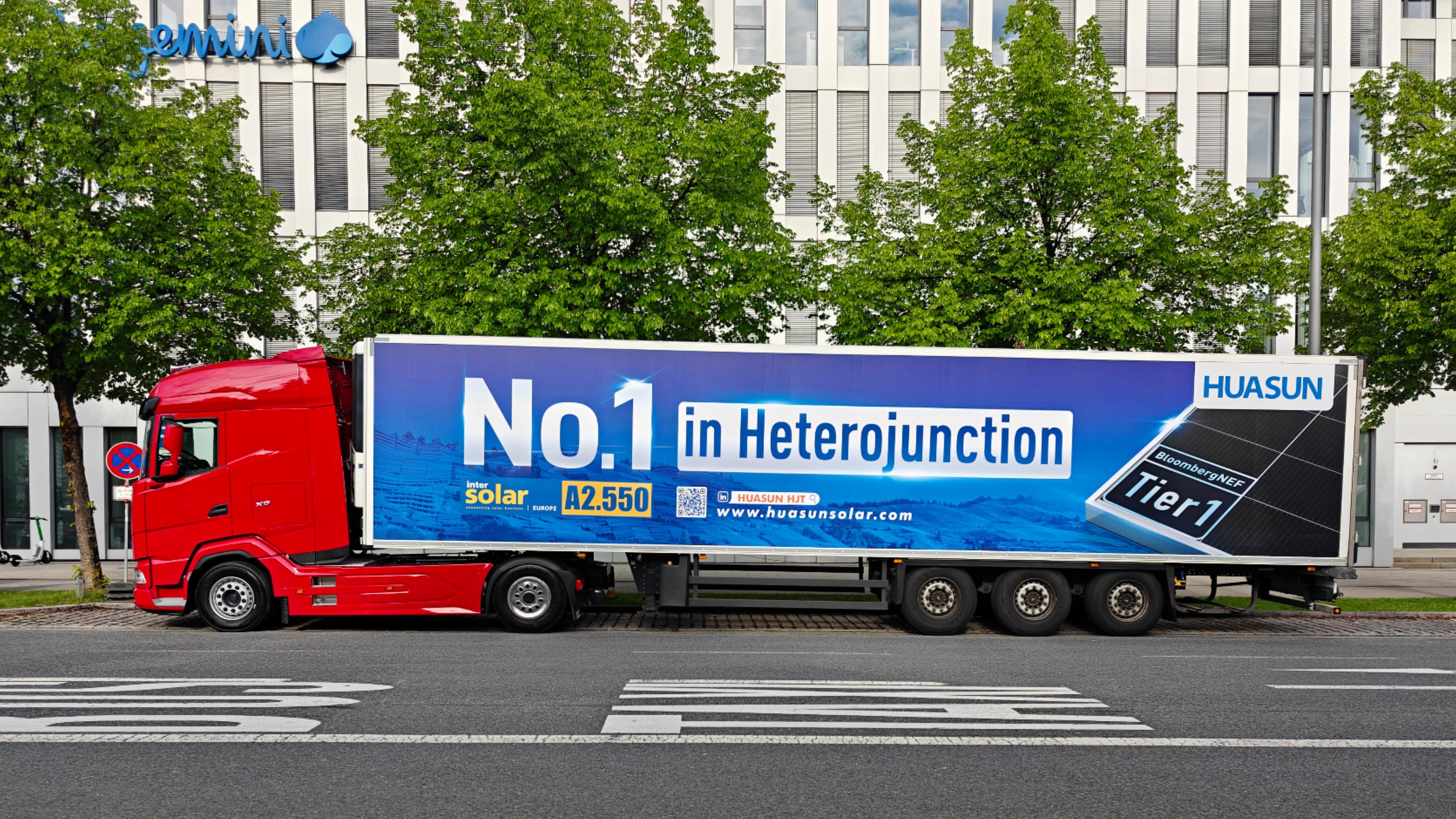
Huasun Wraps Up European Roadshow, Showcasing HJT Leadership and Vertical PV Innovation
2025/07/09
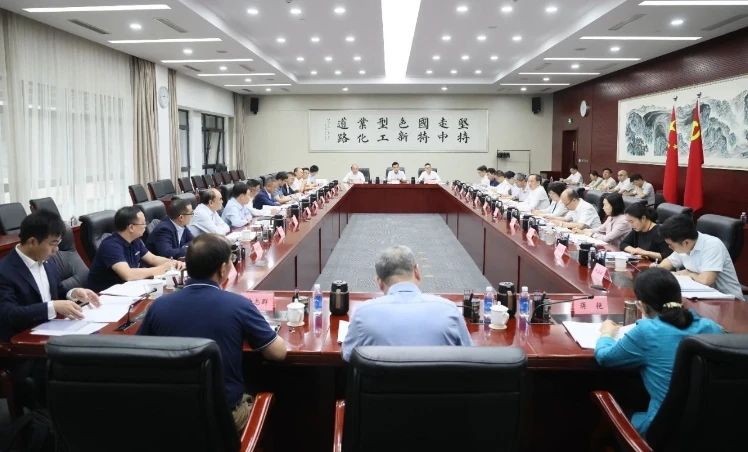
Huasun Energy Attends China’s Ministry-Led Talks to Boost High-quality Solar Growth
2025/07/08

Huasun Stays on Hurun Unicorn List for Third Year Amid Continuous HJT Breakthroughs
2025/07/03
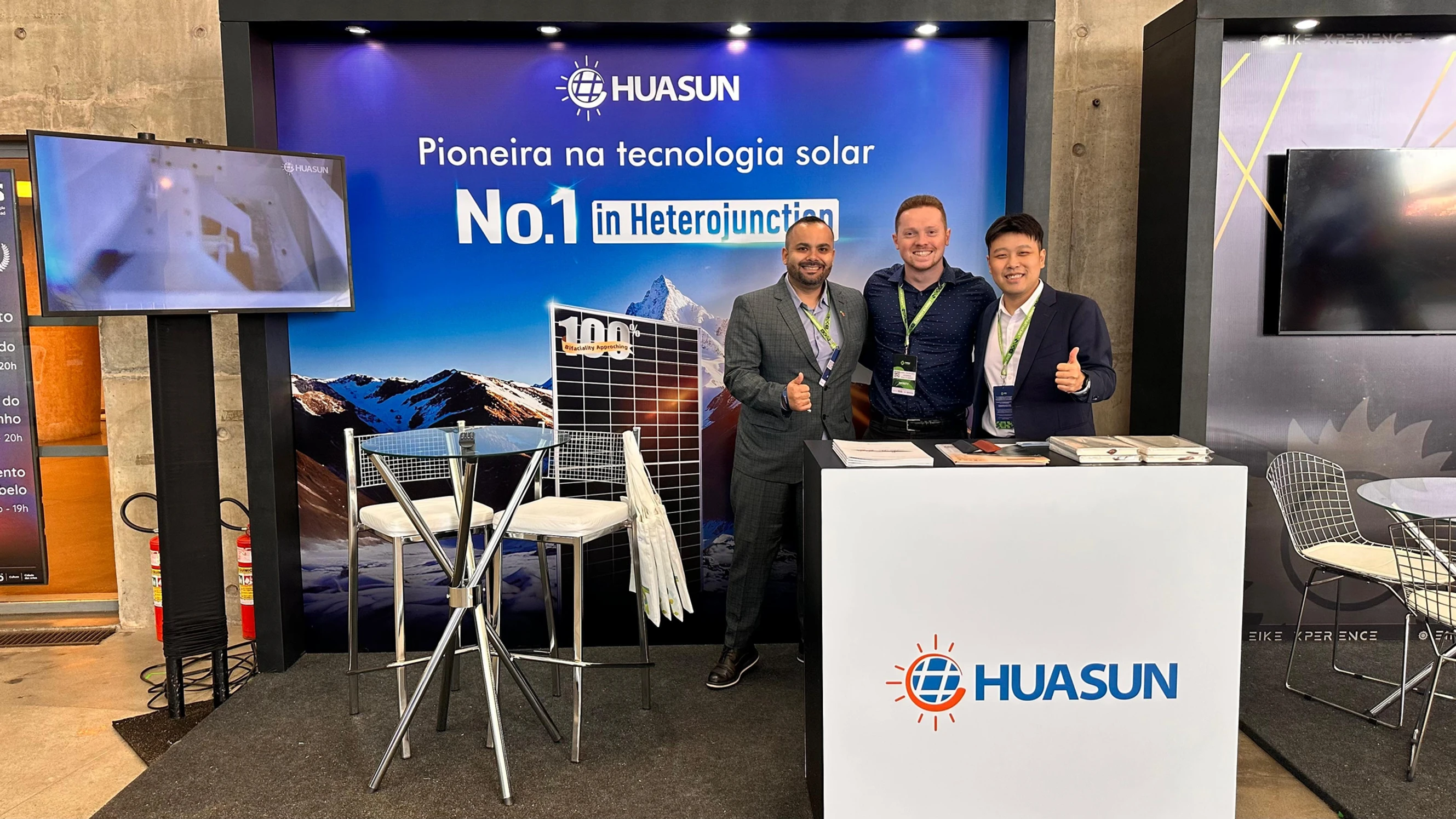
Leading with Heterojunction: Huasun Presents High-Performance Solar Tech at Energy Summit 2025 in Brazil
2025/07/02
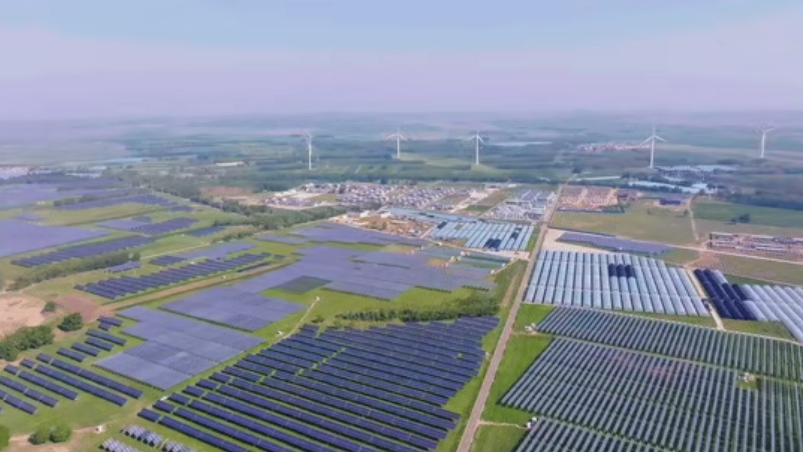
Huasun Wins Bid to Supply 720-740 W HJT Solar Modules for China’s National Hybrid RE Project
2025/07/01